-
Plunger LiftAbstract:
Wellhead effluent is a common problem in the later stages of oil and gas development. With the energy consumption of the reservoir, the gas flow rate is decreasing and the carrying capacity of the gas is continuously weakened.
Details
Wellhead effluent is a common problem in the later stages of oil and gas development. With the energy consumption of the reservoir, the gas flow rate is decreasing and the carrying capacity of the gas is continuously weakened. The plunger gas lift process utilizes reservoir energy to raise the effluent from the bottom of the well to the ground without additional energy and high economy;
The plunger lift system is used in natural gas wells to effectively eliminate bottom water effluent, reduce back pressure on the production layer, prevent flooding, thereby extending the life of natural gas wells; the plunger lift system is used for high oil the weak self-spray or inter-injection wells can effectively utilize the energy of natural gas in crude oil to lift the crude oil in the wellbore to improve oil recovery.
The tool of plunger lift system can effectively eliminate the accumulation of wax, formation salt and scale in the production column, eliminating the need to clean the production wells or remove the crystallization salt and scale operations, which can directly save operating costs.
According to the production wells to prepare the lifting operation program, and has prepared a good lifting program parameters into the automatic controller, through professional software selection for the well of the plunger, the plunger into the well production column, start the controller and run, the plunger from top to bottom run, the bottom of the liquid lifted to the wellhead production pipeline.
The working principle of the plunger is: the plunger in the tubing between the shock absorber spring and the nozzle and then do the cycle of reciprocating motion, the whole system by the controller control pneumatic membrane valve / electric control valve switch to complete. When the pneumatic diaphragm valve / electric control valve is closed, the plunger falls under the action of heavy duty. Plunger down the process at the same time, the bottom hole energy accumulation recovery. When the casing pressure is restored to a certain value, the controller automatically opens the pneumatic diaphragm valve / electrically controlled valve in accordance with the programmed procedure. The gas quickly enters the tubing from the casing / oil annulus and promotes the plunger with the gas generated by the formation The upper liquid slugs move upward until the plunger and its upper fluid are lifted to the ground. The sensor senses the plunger arrives on the ground, passes the arrival signal to the controller, the controller closes in accordance with the preset procedure, and the pneumatic diaphragm valve / solenoid valve closes. The plunger falls under heavy duty and enters the next working cycle.
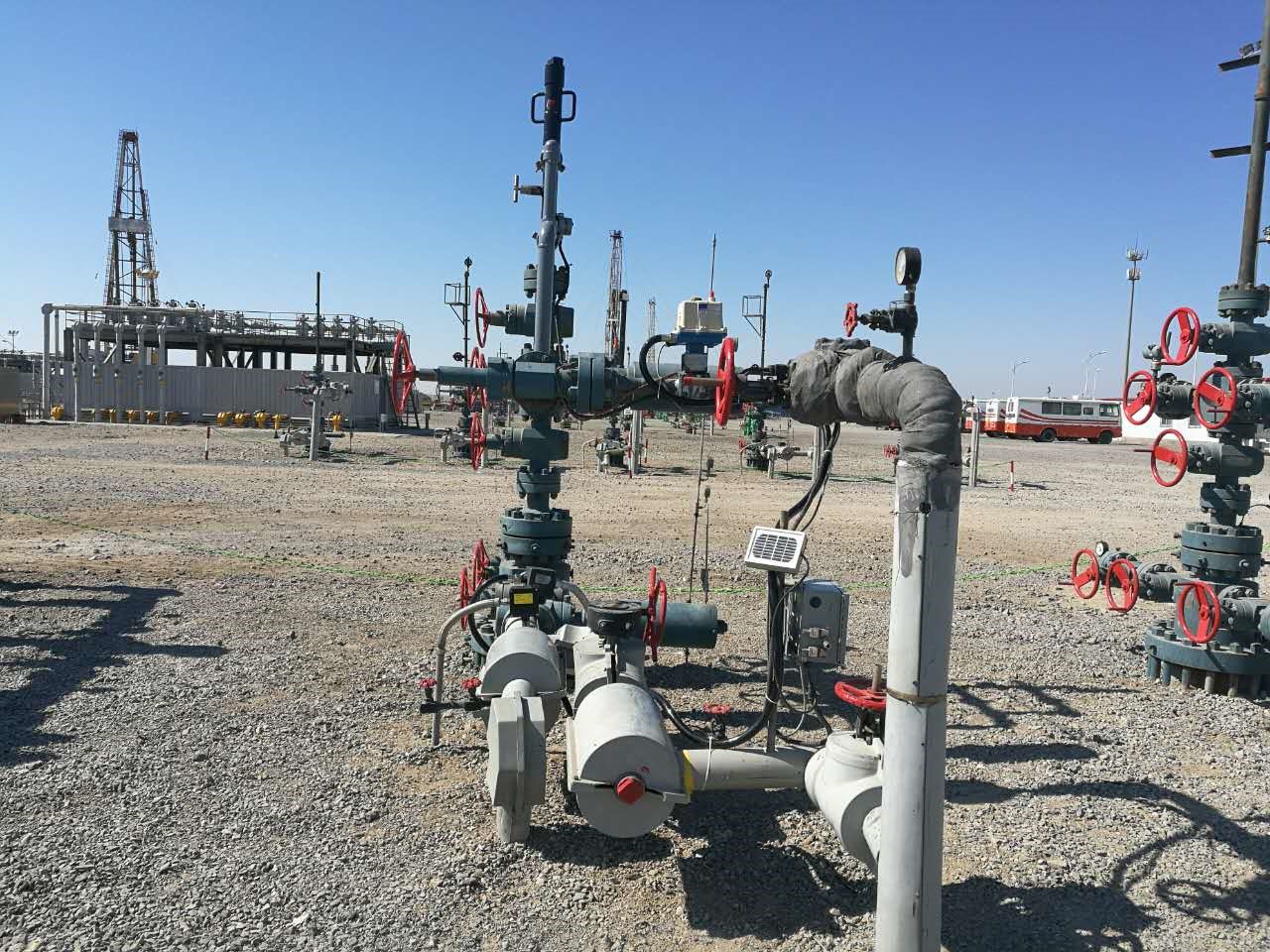
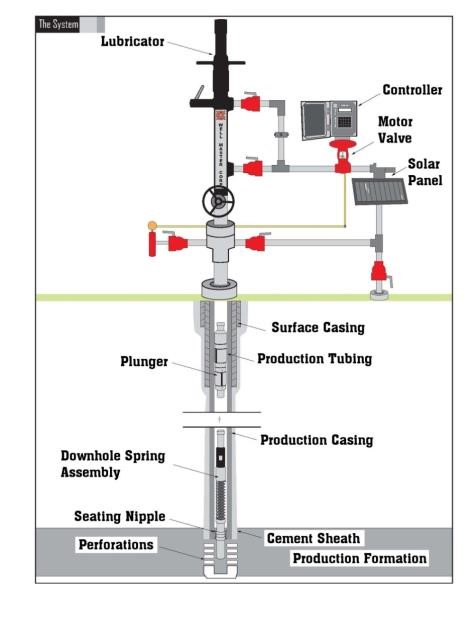
Plunger gas lift working principle diagram
Top Well’s partner in North America-Well masteer began manufacturing and offers plunger gas lift since 1984. In the traditional low pressure, high pressure oil and gas wells, coal bed methane, shale oil and gas fields have a wealth of operating experience.
Top Well provides oil company with a full range of equipment for the installation, installation and post-training of plunger gas lift to maximize production.
First, the scope of the application of plunger technology
To meet the production of one or more of the following conditions can be applied to the plunger lift system:
1. Clear wells in natural gas wells (formation water);
2. High oil to oil ratio;
3. To prevent the formation of wax, salt crystallization or scaling of the wells;
4. Intermittent self sprayed high gas to oil ratio;
5. Large gradient wells;
6. Edge high gas ratio wells;
7. To meet the depth of each 100 meters to produce gas ratio greater than 23.6 (m3 / m3) of the wells.
Second, the advantages of plunger technology
1. Plunger gas lift technology is low cost, long life, is a very high cost of artificial lifting technology (low procurement costs, low installation costs, low operating and maintenance costs, no additional energy consumption);
2. Improve the efficiency of production wells;
3. Save wax cleaning costs;
4. Don’t need additional energy which is additional energy costs are saved;
5. Make most of the failure of the wells to resume production;
6. Slow down the production wells;
7. Extend the production cycle of the production wells.